I plan to weld 50 mm OD stainless pipe but the pipe on the R1 can is 60 mm OD.
Is it ok to put the smaller pipe inside the can and then use strips of stainless bent into a circle to pad it out or am I better getting the 50 mm flared out so it is a tightish fit inside the other pipe and then weld that (no packing pieces)?
How did you do this if you had the same problem?
BTW I wouold be using MIG, with stainless wire.
Hello Guest User,
Please feel free to have a look around the forum but be aware that as an unregistered guest you can't see all of it and you can't post.
To access these 'Registered Users Only' areas simply register and login.
Please feel free to have a look around the forum but be aware that as an unregistered guest you can't see all of it and you can't post.
To access these 'Registered Users Only' areas simply register and login.
welding stainless steel exhaust pipe
Moderators: paul doran, Taffus, KeithZ1R, chrisu
- paul doran
- Area Rep.
- Posts: 9141
- Joined: 24th Sep 2004
- Location: near Dublin Ireland
- Exhaust Craft
- 100Club
- Posts: 201
- Joined: 17th Feb 2008
- Location: Whitehaven Cumbria
- Contact:
No
If you want send me both bits and i will expand the 50mm tube so the 60mm tube will slide over it perfect,please do not mig it,it will turn out looking crap.
Dave wwwexhaustcraft.co.uk
Dave wwwexhaustcraft.co.uk
^^^ thanks for the offer, Most generous
but I am not that fussed about looks - the carbon can has aluminium caps at each end that should hide the messy weld.
I haven't got the pipe I want to attrch to it yet ... and postage, to you and bakc would be more than I paid for the can (ebay) and probs may find someone local to me but I'd like to have a go myself.

I haven't got the pipe I want to attrch to it yet ... and postage, to you and bakc would be more than I paid for the can (ebay) and probs may find someone local to me but I'd like to have a go myself.
- Exhaust Craft
- 100Club
- Posts: 201
- Joined: 17th Feb 2008
- Location: Whitehaven Cumbria
- Contact:
Are you any good at sheet metal development? You could try rolling a cone out of sheet.
Your flat blank will look like this
A rough way to calculate the rads and angle is to us the following – d1 and d2 are you finished diameters and L is the length of the cone. The inner radius that will form the small end of the cone is worked out as – the small dia multiplied by the length (d1 x L ) then divide that by the difference between the two diameters ( d2 – d1 )
The angle (angles are always difficult) is 180 times the small dia times the difference in diameters ( 180 x d1 x ( d2 – d1 ). Then divide that by the small dia times the length ( d1 x L ).
So for a cone of 50mm to 60mm by 30mm long your sums will be
Radius = 50 x 30 / 60 – 50 = 150
Angle = 180 x 50 x (60 – 50) / 50 x 30 = 60 degrees
This is only a rough guide as it doesn’t take account of material thickness or welding allowance but if you cut it out of a piece of paper first you will see if you’re on the right track.
All you need now are some bending rolls to go with your welder.
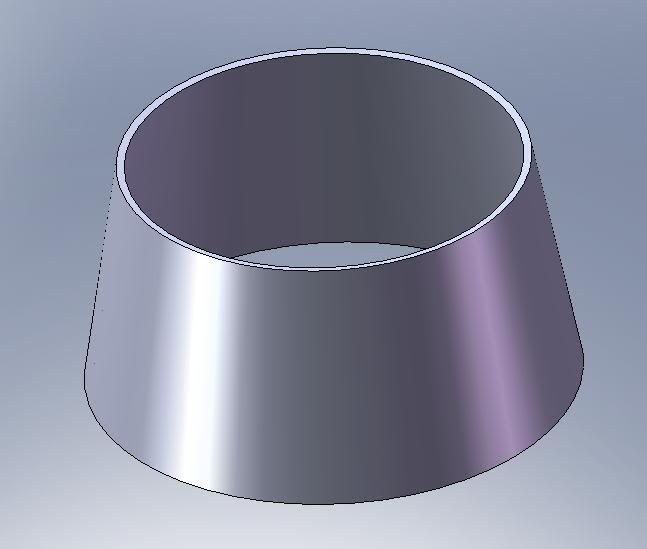
Your flat blank will look like this
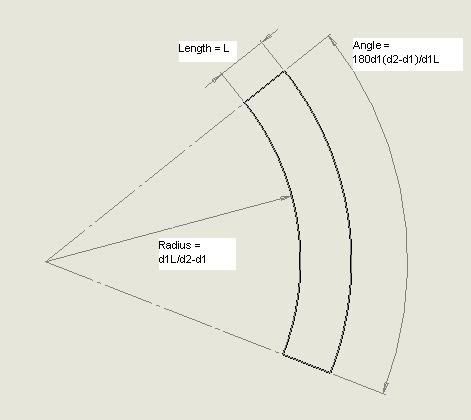
A rough way to calculate the rads and angle is to us the following – d1 and d2 are you finished diameters and L is the length of the cone. The inner radius that will form the small end of the cone is worked out as – the small dia multiplied by the length (d1 x L ) then divide that by the difference between the two diameters ( d2 – d1 )
The angle (angles are always difficult) is 180 times the small dia times the difference in diameters ( 180 x d1 x ( d2 – d1 ). Then divide that by the small dia times the length ( d1 x L ).
So for a cone of 50mm to 60mm by 30mm long your sums will be
Radius = 50 x 30 / 60 – 50 = 150
Angle = 180 x 50 x (60 – 50) / 50 x 30 = 60 degrees
This is only a rough guide as it doesn’t take account of material thickness or welding allowance but if you cut it out of a piece of paper first you will see if you’re on the right track.
All you need now are some bending rolls to go with your welder.
A2 1979-80. A1 1980-now
Who is online
Users browsing this forum: No registered users and 123 guests